Rubber rollers for printing machines in India
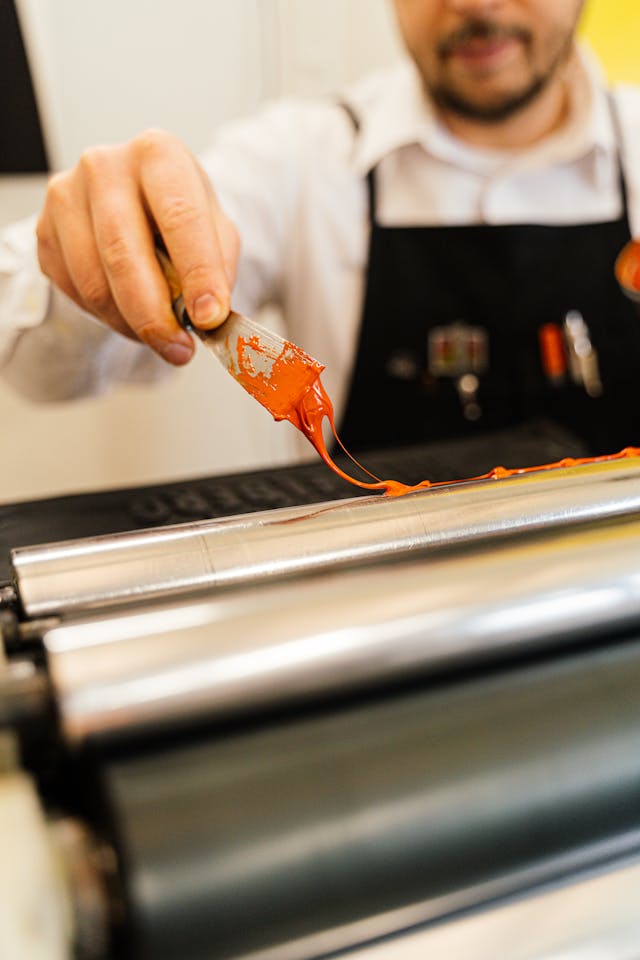
Rubber rollers for printing machines in India
Rubber rollers purpose, selection, and suppliers
A rubber roller is one of the key elements in printing, ensuring accuracy, quality and stability of the printing process. In modern printing enterprises in India , these components play a critically important role, especially in large-scale and high-precision printing. In this material, we will consider in detail what rubber rollers for printing machines are, what their functions are, what types there are, what to look for when choosing, and where in India you can buy high-quality rubber rollers.
What is a rubber roller for a printing machine?
A rubber roller is a cylindrical element that is covered with a special rubber or polymer layer and installed in a printing machine. Its main function is to transfer ink or dampening solution to the printing plate or directly to the printed material (paper, cardboard, etc.).
Depending on the type of printing machine (offset, flexographic, gravure, etc.), the design and properties of rubber rollers may differ slightly. However, they must all meet high standards of wear resistance, chemical resistance to inks and solvents, and ensure uniform ink distribution.
Main types of rubber rollers
Various kinds of rubber rollers are employed across different types of printing equipment:
1. Ink rollers
Their main function is to deliver ink from the inking system directly onto the printing plate. Such rollers must be as resistant as possible to mechanical abrasion and the effects of inks.
2. Dampening rollers
These elements supply a dampening solution to the printing plate. They must be compatible with water-alcohol and other dampening systems.
3. Form rollers
These are rollers that are in direct contact with the printing plate, so the accuracy of printing depends on their quality.
4. Pick-up and Transfer Rollers
These rollers facilitate the movement of paper and other substrates throughout the printing operation.
Although they may not be completely rubber, they often have a rubber coating for better grip.
Key characteristics of a quality rubber roller
When choosing a rubber roller for a printing machine, you should pay attention to the following parameters:
The Shore hardness of the rubber coating indicates its elasticity and helps determine its appropriateness for specific printing applications.
Chemical resistance – the roller must be compatible with the types of inks used in production.
Geometric accuracy – the correct shape and balancing of the roller prevents vibrations and printing defects.
Wear resistance – the rollers must withstand many hours of load without losing their characteristics.
The possibility of regeneration – some models allow repeated application of the rubber layer, which reduces operating costs.
Advantages of using quality rubber rollers
Investing in quality rubber rollers is not just a cost, but a way to increase the efficiency of the printing process:
Improving print quality – a uniform layer of ink, image clarity, no spots and streaks.
Reduced equipment downtime – quality rollers require less replacement or maintenance.
Reduced ink costs – optimal ink application allows for less ink to be used.
Longer plate life – soft and stable adhesion to the plate reduces wear.
How to choose a rubber roller for your printing machine?
Prior to buying a rubber roller, it’s essential to take into account the following factors:
Type of printing machine (format, manufacturer, model)
Type of printing (offset, flexo, pad printing, etc.)
Inks and solvents used
Print volume – for large runs, you should choose highly wear-resistant models.
Possibility of consulting with technical specialists – some suppliers provide selection, installation and adjustment services.
How much does a rubber roller cost in India?
The price of a rubber roller depends on the size, type of coating, purpose and manufacturer. Average cost:
Paint rollers – from 1000 to 3,000 Rs
Wetting rollers – from 600 to 2,500 Rs
Individual rollers to order – from 2,500 Rs and above
Recovery/recoating of the roller – from 1,000 Rs
Costs can fluctuate based on currency exchange rates, material expenses, and the intricacy of the order.
Tips for caring for rubber rollers
To make the roller last as long as possible, follow these simple rules:
Regularly clean the roller from paint and dust residues
Use only recommended solvents
Avoid prolonged contact with aggressive chemicals
Store the rollers in a dry environment at a constant temperature
Perform a preventive inspection at least once a month
A rubber roller plays a crucial role in all printing machines, serving as a key element that directly impacts both print quality and operational efficiency. In today’s Ukrainian market, a large number of options are available – from budget models to premium imported solutions. The main thing is to choose the right type of roller for your technology and contact trusted suppliers. Regular maintenance, high-quality installation and compliance with technological standards are the key to long-term and stable operation of your printing equipment.
Personalized support
We’re here to help you! Reach out to us. We are available via email to answer all your questions