Alcohol-damping Rollers Manufacturers and Suppliers in India
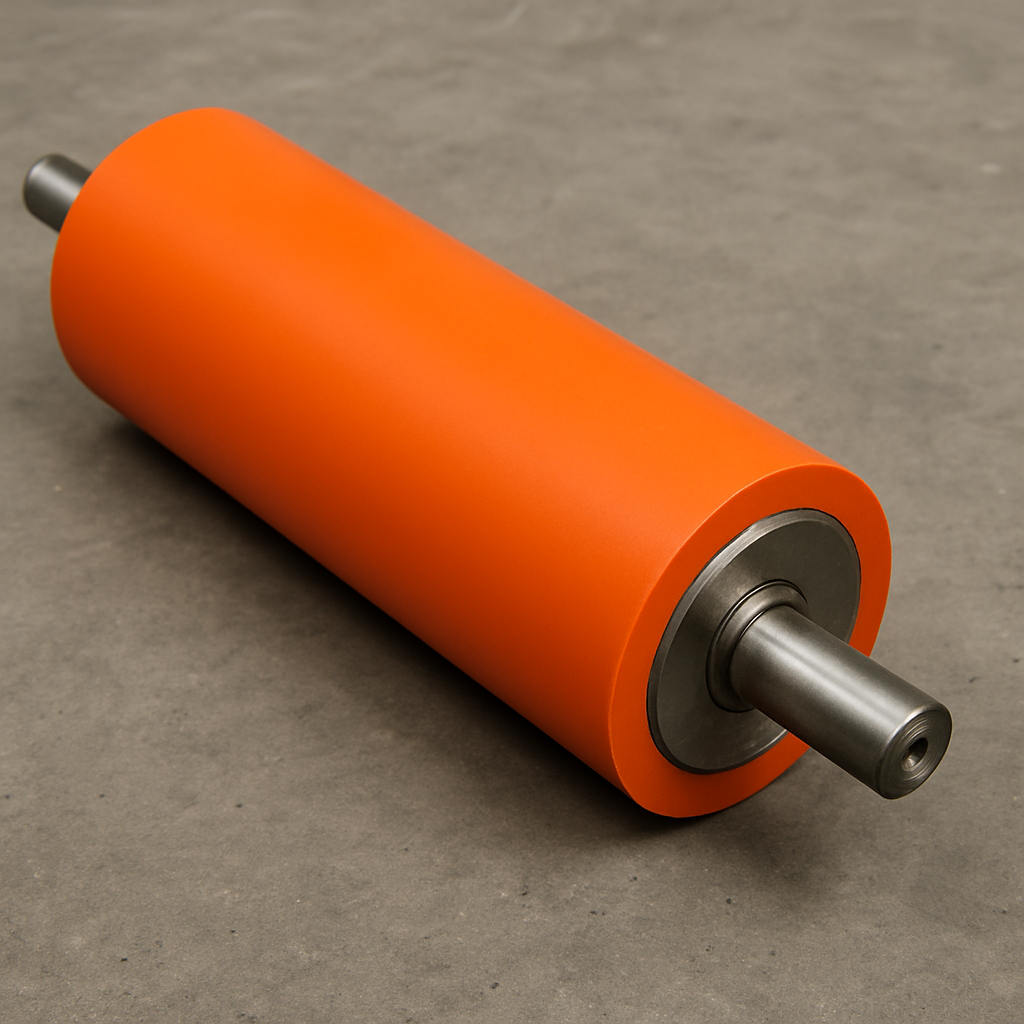
Alcohol-damping rollers for printing machines in India
Premium Alcohol-Dampening Rollers – Trusted Manufacturers & Suppliers in India
In the dynamic world of offset printing, every component plays a vital role in determining print quality, efficiency, and cost-effectiveness. One of the most critical yet often underappreciated parts is the alcohol-dampening roller. As a top-tier producer and trusted supplier of alcohol-dampening rollers in India, we are committed to providing high-efficiency solutions that boost printing press performance and deliver outstanding print quality.
Whether you’re running small-format offset machines or high-speed commercial presses, our alcohol-dampening rollers are engineered to meet the highest standards of precision and durability. Let’s explore what sets our rollers apart, why they’re essential, and why we are the go-to supplier for printing professionals across India.
What Are Alcohol-Dampening Rollers?
Alcohol-dampening rollers are specialized components used in offset printing machines, especially those that employ the alcohol-based dampening system. These rollers play a crucial role in transferring the fountain solution (a mixture of water, isopropyl alcohol, and other additives) onto the plate cylinder. This dampening solution is designed to keep the non-printing areas of the plate properly hydrated, preventing ink from adhering and helping to preserve sharpness and accuracy in the final print.
The alcohol in the solution enhances evaporation, stabilizes pH, and reduces surface tension, helping printers achieve sharper images with minimal dot gain. The roller must be able to distribute the solution evenly, resist chemical wear, and perform consistently under demanding pressroom conditions.
Why Choose Our Alcohol-Dampening Rollers?
1. Precision Engineering
We design and manufacture each roller with precision, using advanced rubber compounds and state-of-the-art machinery. The balance, surface finish, and roundness of each roller are tested rigorously to ensure optimal performance on every type of offset press.
2. Superior Material Composition
Our alcohol-dampening rollers are made from high-grade, chemically resistant rubber compounds that offer excellent compatibility with alcohol-based dampening solutions. These materials resist swelling, hardening, or chemical breakdown, even under prolonged exposure.
3. Longer Service Life
One of our key advantages lies in the longevity of our rollers. We understand that printers need durable components to minimize downtime and reduce maintenance costs. That’s why our rollers are built to offer extended service life without compromising on quality.
4. Perfect Fit for All Leading Presses
We supply rollers compatible with top printing press brands including Heidelberg, Komori, Mitsubishi, Ryobi, Manroland, and others. Whether you’re operating sheetfed, web offset, or newspaper presses, we provide customized rollers that perfectly match your machine specifications.
5. Consistent Performance
Thanks to our strict quality control process, every roller we produce ensures smooth operation, consistent dampening, and improved ink-water balance. Our rollers reduce start-up time, paper waste, and minimize ghosting or streaking issues in prints.
Key Benefits of Using High-Quality Alcohol-Dampening Rollers
-
Improved Print Clarity: Uniform dampening helps maintain sharp image reproduction.
-
Enhanced Ink-Water Balance: Proper transfer of dampening solution ensures consistent ink behavior on press.
-
Reduction in Paper Waste: A properly functioning dampening system reduces misprints and waste.
-
Lower Press Downtime: Reliable rollers result in fewer press stoppages and less maintenance.
-
Cost Savings: Reduced need for frequent roller replacements means long-term operational savings.
Applications Across the Printing Industry
Our alcohol-dampening rollers are trusted by a wide range of industries, including:
-
Newspaper printing
-
Commercial printing
-
Packaging and label printing
-
Book and magazine publishing
-
Security and currency printing
No matter the size of your operation, our dampening rollers provide the consistency and performance you need to stay competitive in today’s fast-paced printing environment.
Why We Are the Best Manufacturers and Suppliers in India
Decades of Expertise
With years of experience in the rubber roller manufacturing industry, our team understands the evolving needs of offset printers and continues to innovate with new materials and designs.
Made in India, Trusted Worldwide
Our production facilities are equipped with modern manufacturing equipment and staffed by trained engineers who uphold international quality standards. While we proudly manufacture in India, our products meet global performance benchmarks.
ISO-Certified Quality
We follow strict quality management systems and are ISO-certified to ensure that every batch of rollers is consistent, reliable, and safe for use in critical printing operations.
Fast Turnaround Times
We know that time is money in the printing business. Our in-house production and logistics systems enable us to deliver customized orders quickly, often faster than imported alternatives.
Exceptional Customer Support
From pre-sales advice to post-sales support, our dedicated team works closely with clients to ensure satisfaction at every stage. We also provide roller reconditioning and maintenance guidance to extend product life.
Roller Reconditioning Services
In addition to new roller manufacturing, we offer professional roller reconditioning services. If your current alcohol-dampening rollers are worn but the cores are still in good condition, we can refurbish them with new rubber covering, saving you significant cost without compromising performance.
Custom Orders and Bulk Supply
We cater to both individual press owners and large commercial printing houses. If you require bulk quantities or have unique press requirements, our team can develop customized alcohol-dampening rollers tailored to your machine type, climate conditions, and print substrates.
We serve clients across major printing hubs such as Delhi, Mumbai, Chennai, Kolkata, Hyderabad, Ahmedabad, and more. Our extensive distribution system enables us to deliver orders swiftly and reliably to every corner of India.
Order Alcohol-Dampening Rollers from the Best in India
At [Dr.WEBSEO], we are more than just a supplier—we are your printing performance partner. We stand by the quality of our alcohol-dampening rollers, which are backed by technical expertise, superior materials, and a deep commitment to customer satisfaction.
Don’t compromise on print quality. Choose the alcohol-dampening rollers that industry leaders trust.
Personalized support
We’re here to help you! Reach out to us. We are available via email to answer all your questions
Alcohol-Dampening Rollers – FAQ Guide for Printing Professionals
Alcohol-dampening rollers are an essential component in the offset printing process, yet many professionals still have questions about their purpose, maintenance, and selection. Whether you’re new to offset printing or a seasoned press operator, understanding how alcohol-dampening rollers function can help you improve print quality, reduce downtime, and extend the life of your printing equipment.
As a top manufacturer and supplier of alcohol-dampening rollers in India, we’ve compiled this comprehensive FAQ to answer the most common questions and help you make informed decisions for your pressroom.
1. What is an alcohol-dampening roller?
An alcohol-dampening roller is a rubber-coated roller used in offset printing machines to apply a dampening solution to the printing plate. The mixture—comprising water, isopropyl alcohol, and specific additives—helps maintain moisture in the non-printing zones of the plate. As a result, ink adheres only to the image areas, producing clean, sharp prints.
2. Why is alcohol added to the dampening solution?
Isopropyl alcohol (IPA) serves multiple important functions within the dampening solution:
-
It lowers the surface tension of water, enabling smoother flow across the roller surface.
-
It helps the solution evaporate faster, which is especially useful for high-speed printing.
-
It contributes to better ink-water balance on the plate, improving overall print stability.
3. How do alcohol-dampening rollers improve print results?
When functioning correctly, these rollers:
-
Maintain consistent moisture levels across the plate.
-
Help prevent ink from spreading into non-image areas.
-
Support clean transitions between print runs.
-
Minimize print defects like streaks, ghosting, and scumming.
In short, they help printers achieve better image clarity, color consistency, and print accuracy.
4. What materials are used in making these rollers?
Premium alcohol-dampening rollers are manufactured using advanced rubber materials specifically formulated for performance and durability. These materials are chosen for their ability to resist chemical reactions, withstand wear, and maintain surface integrity over time. Common materials include:
-
Nitrile-based compounds
-
EPDM, short for Ethylene Propylene Diene Monomer, is a synthetic rubber known for its resistance to heat, weather, and chemicals.
-
Other custom-engineered synthetic blends
The rubber material selected has a significant impact on how long the roller lasts and how well it performs with alcohol-containing dampening fluids.
5. Which printing machines use alcohol-dampening rollers?
These rollers are used in a wide range of offset printing machines, including:
-
Sheet-fed presses
-
Web offset presses
-
Newspaper printing equipment
-
Commercial and packaging presses
They are particularly suited for presses that operate at higher speeds or where precision and consistency are critical.
6. How often should alcohol-dampening rollers be replaced?
Roller lifespan depends on several factors:
-
Type and quality of the rubber
-
Frequency of use
-
Maintenance routines
-
Press operating conditions
Generally, dampening rollers last between 12 and 18 months. However, some may need replacement sooner if they show signs of wear, hardening, or surface damage.
7. How can I tell if a roller needs replacing?
Common indicators that a roller may need replacement include:
-
Ink-water balance issues
-
Irregular dampening or dry spots
-
Glazing or hardened surface
-
Surface damage such as splits, bulging, or noticeable wear
-
Higher levels of paper spoilage or inconsistent print results
If your press is experiencing any of these symptoms, it’s advisable to inspect the roller condition and consider replacement or reconditioning.
8. Is it possible to recondition alcohol-dampening rollers?
Yes, many rollers can be reconditioned if the core is still in good shape. The process involves removing the old rubber layer, applying a new compound, and grinding the surface to the required finish. Reconditioning is a cost-effective solution, extending the life of the roller and reducing the need for frequent replacements.
9. How should these rollers be maintained?
Proper care of dampening rollers ensures longer service life and consistent print performance. Follow these tips:
-
Clean rollers thoroughly after each press run.
-
Use recommended cleaning agents that are compatible with alcohol-based solutions.
-
When not in operation, keep the rollers in a dry, temperature-controlled environment to preserve their condition.
-
Avoid using sharp objects or abrasive materials during cleaning.
Routine checks for surface wear and chemical buildup can help detect issues before they impact production.
10. What are the consequences of using poor-quality rollers?
Using low-grade or worn-out rollers can lead to:
-
Inconsistent ink transfer
-
Print defects and increased waste
-
Frequent press downtime
-
Higher operating costs due to frequent replacements
Choosing top-grade rollers leads to more efficient performance, improved print quality, and reduced expenses over time.
11. Can you supply rollers for all types of printing presses?
Absolutely. We manufacture and supply alcohol-dampening rollers compatible with a wide range of press models including:
-
Heidelberg
-
Komori
-
Ryobi
-
Manroland
-
Mitsubishi
-
And others
Whether your machine is sheet-fed, web-based, or custom-built, we can provide rollers that match your specifications.
12. Do you offer custom roller solutions?
Yes. We specialize in designing and manufacturing custom alcohol-dampening rollers based on your exact press requirements. If you have specific dimensions, rubber hardness, or performance needs, our engineering team can develop the right solution for you.
13. How fast can I receive a roller order?
We maintain a well-organized distribution system across India to ensure quick and reliable delivery. For standard models, delivery can often be completed within a few working days. Custom orders may require additional time for production, but we always prioritize timely fulfillment.
14. How does your company ensure quality in roller production?
Quality is at the heart of our manufacturing process. Each roller undergoes:
-
Material inspection
-
Precision machining
-
Surface finish checks
-
Chemical resistance testing
Our production follows strict quality control standards to ensure you receive rollers that perform consistently and reliably on press.
15. Why choose us as your roller partner in India?
Here’s why thousands of printing professionals trust us:
-
Extensive industry experience
-
Advanced production facilities
-
Use of high-quality materials
-
Custom manufacturing capabilities
-
Quick delivery across India
-
Strong technical support team
Whether you’re looking for replacements, bulk orders, or custom designs, we provide roller solutions that add value to your printing operations.